Advantages of Chemical Polishing for Stainless Steel
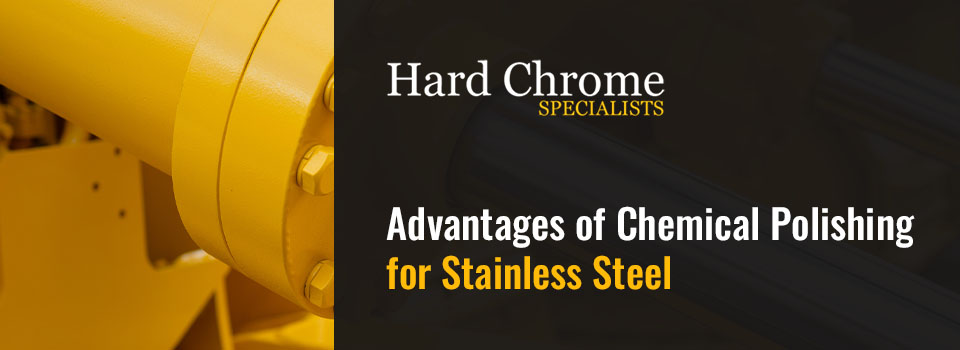
Polishing is an important finishing step that helps eliminate imperfections and impurities from stainless steel and other metal surfaces. It improves the appearance or aesthetics of stainless steel parts by creating smooth and shiny surfaces. It also improves functionality by preventing contamination caused by corrosion, oxidation and high temperatures during processing.
Chemical polishing is among the three main stainless steel methods, including electrochemical and mechanical polishing. The three have numerous advantages and disadvantages, which we explore below to help you choose the best method for your next stainless steel project.
How Chemical Polishing Stainless Steel Works
Chemical polishing or passivation is a popular finishing process for stainless steel that involves dipping stainless steel parts into an alkaline or acidic solution. Citric acid and nitric acid are two of the most commonly used chemical polishing solutions.
The stainless steel part is cleaned to remove grease, dust, dirt, oil and other contaminants before being submerged in the solution. When submerged, the solution etches and levels the metal surface to dissolve the surface roughness and result in a bright, reflective surface finish. Different chemical solutions are suitable for different stainless steel grades because they have unique corrosion development patterns.
This process dissolves the upper layer of a stainless steel part, enabling fast smoothing of micro-roughness instead of achieving the perfect surface. Chemical polishing removes blurs, etches, leveling, vapor stains, debris, surface defects and microscopic particles. It also fills in micro crevices to improve the surface texture.
It results in the formation of a passivation layer, which is an iron-free layer with passive nickel or chromium properties that prevent further corrosion or contamination. The parts often need a final rinse-off, typically using a neutralization bath to improve the passivation results.
Chemical Polishing Benefits
Chemical polishing for stainless steel has numerous benefits for stainless steel parts:
- It allows the polishing of complex-shaped workpieces and components.
- It’s an affordable polishing method that doesn’t require specialized fixtures or a DC power source.
- It’s a highly efficient process that allows multiple stainless steel parts to be polished simultaneously.
- It provides an ultraclean surface finish.
- It improves the localized corrosion and mechanical strength plus extends the service life of stainless steel workpieces.
- It allows control over the level of protection on the surfaces.
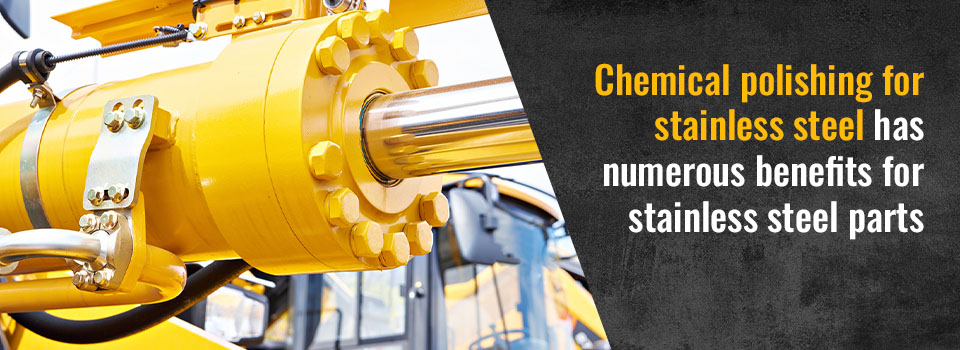
At the same time, chemical polishing has some drawbacks that make it less desirable for specific applications. Some of these drawbacks include:
- It results in inconsistent or uneven brightness on the surface of the workpiece.
- The chemical polishing solution is difficult to heat to the accurate temperature that produces the best results.
- It’s hard to adjust and regenerate the chemical polishing solution.
- The chemical polishing solution produces harmful gases for humans and the environment, such as nitrogen oxide.
Mechanical Polishing vs. Electropolishing
Mechanical polishing is a finishing process that involves using abrasives to smooth surfaces. It exposes metal grain and often results in scratches, stains and embedded abrasives that cause future points of corrosion. Auxiliary tools such as turn tables improve the mechanical polishing results. It utilizes abrasives of increasing grit to achieve a fine surface finish and allows a high degree of customization.
The advantages of mechanical polishing are:
- It requires highly skilled craftsmanship, which increases the quality of the finish
- Allows greater customization
Disadvantages of mechanical polishing include:
- It’s a time-consuming process that requires attention to detail
- The high time and labor requirements make it more expensive
- There’s an increased risk of human error transferred to the stainless steel surface
Electrochemical polishing or electropolishing uses a phosphoric electrolytic solution in which the stainless steel are submerged and a current is passed through. The current attracts the metal ions on the stainless steel part to remove them. It is then rinsed and dried to eliminate any remaining metal ions. It eliminates a uniform layer of surface material, impurities and contaminants, resulting in a smooth and blemish-free polished surface.
Advantages of electropolishing:
- Produces consistent results across the entire surface of complex workpieces
- Enhances stainless steel’s resistance to corrosion by eliminating impurities and contaminants
- Removes the heat tint or oxide scale produced during welding or heat treating to produce a bright and shiny aesthetic finish
- Minimizes the microfinish values for complex parts by removing an even layer of surface material
Some disadvantages of electropolishing include:
- It involves a complex pre-polishing process
- It can be expensive because it requires the use of specialized equipment and processes
- It removes material from the surface of a stainless steel part, making it thinner and weaker
Electropolishing vs. Chemical Polishing
Electrochemical polishing is preferred over chemical polishing for critical stainless steel parts because it finishes surfaces with a high level of precision and consistency. The resulting surface is much more corrosion-resistant than the passivation layer formed through chemical polishing. Electropolishing produces a brighter and shinier stainless steel surface than chemical polishing because it removes all surface impurities, including debris, scale and oils.
Electropolishing vs. Mechanical Polishing
Electropolishing eliminates the need for mechanical metal finishing processes, such as cleaning, tumbling, pickling and hand deburring. Electropolishing is faster and more efficient than mechanical polishing. It also reduces waste production by removing a minimal amount of surface material, which results in workpieces that meet higher cleanliness standards than the latter. Unlike chemical resistance, electropolishing enhances the corrosion resistance and stress life of the metal.
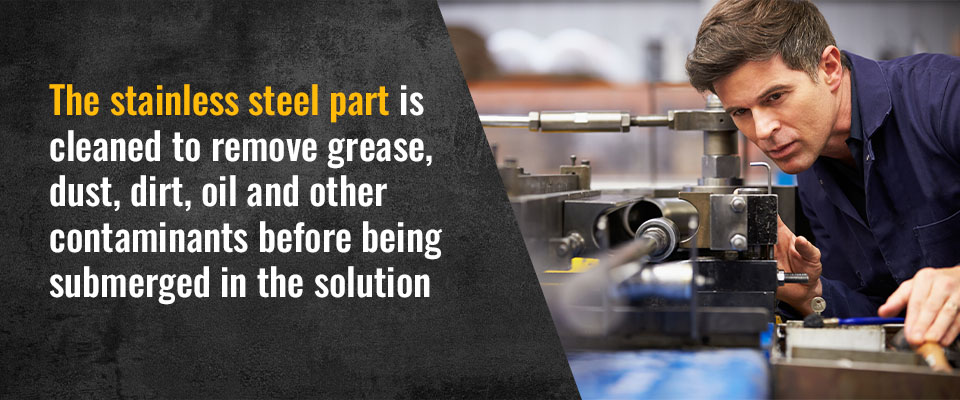
Is Electropolishing Better Than Mechanical Polishing?
Electropolishing is better than mechanical polishing in many ways — it’s faster, more efficient, minimizes waste production and enhances corrosion resistance, fatigue life and cleanliness standards of stainless steel work pieces.
Is Electropolishing Better Than Chemical Polishing?
Electropolishing produces higher-quality and brighter surfaces than chemical polishing. It also produces a significantly more corrosion-resistant layer than the latter. However, electropolishing produces thinner and weaker stainless workpieces than chemical polishing because it removes some surface material. Chemical polishing may also be preferable when your budget is limited because it’s less expensive than electropolishing.
Get Superior Stainless Steel Polishing Services
Hard Chrome Specialists is a family-owned company in PA that’s been offering commercial and industrial metal finishing services since 1988. We offer electropolishing and chemical polishing services to clients in various industries looking to create corrosion-resistant stainless steel surfaces. Our experience and expertise ensure we provide you with custom products that satisfy your needs and meet your part requirements.
Looking for more information about stainless steel surfaces? Contact us today to have one of our friendly representatives answer your questions and advise you on the best polishing service for your unique needs.